Lews Castle College's Will Lamb, who called in the SOS team to track down the causes of some peculiar issues in the College studio.
This month we journey to the Outer Hebrides, where a college teaching Gaelic music has more than a few wires crossed...
Will Lamb is a certified Pro Tools instructor who teaches at Lews Castle College Benbecula, Lionacleit, on the Isle of Benbecula, which is one of the Uist group of islands in the Outer Hebrides. This area is known for its high-quality output of traditional music, so it's no surprise that the focus of the college studio is on the recording of Gaelic music and the teaching of recording principles.
Will is American by birth, but moved to Nova Scotia in Canada, where he learned Gaelic, before moving to the Hebrides. He asked Sound On Sound if we'd be prepared to fly up and visit his studio to help him sort out some problems in one of the College's studios, and also to talk to his students, most of whom were serious musicians wanting to learn how to record their work. We agreed, so in March we found ourselves on a prop-driven plane heading for Benbecula, a windswept, low-lying island, where it seemed nobody would dare build a wind farm in case it blew away. Most of the island, which is steeped in history, salt water and single-malt whisky, stays above water at low tide except on particularly bad days, and although the wind sock was horizontal most of the time this was clearly a good day. We now understand why so many of the local musicians choose to play the Uillean pipes — they double as an emergency flotation device, which can be topped up by blowing into the tube, and a chanter is provided for attracting attention!
School Report
After an introductory cup of coffee and a choice of Hob Nobs, Will told us a little about the course, and also outlined some of the issues he needed to tackle. The Pro Tools-based studio was installed in a room that had been built and wired by contractors and, as is so often the case, the builders and electricians knew little about the requirements of audio or, indeed, the correct way to wire audio cables. This meant that Will inherited a few problems along with his new studio — some of which proved pretty tricky to track down.
The most vexing of these problems was associated with the headphone monitoring. This was provided by a Samson Q4 headphone amplifier, connected to the studio via a TRS tie-line and plugged into the Cue outputs of the Presonus Central Station that was being used as a monitor controller. Will explained that the headphone mix seemed almost mono, but not quite, and that panning channels produced strange results.
The line-level stereo source was connected via a quarter-inch socket Y-cord, which accepted two unbalanced input jacks, and routed them to a single TRS jack to provide an unbalanced stereo feed. This was then connected via a TRS plug on a tie-line through to the studio wall-box, where a long lead converted the stereo TRS to two unbalanced mono jacks, which were connected to the Samson headphone amp.
Wired For Weird
It isn't just pupils that misbehave in college — this Samson Q4 headphone amp was producing strange results. Eventually they turned out to be caused by wiring problems.Unplugging the jacks feeding the Y-cord produced very strange results, so we brought the Samson headphone amp into the control room and tried feeding it directly from the Central Station. That worked perfectly, so we re-tested with the Y-cord and TRS-to-double-TS Y-lead from the studio. Again, it worked perfectly, which suggested that the fault lay in the tie-line wiring.
In removing the wall-box plate, we discovered that the screen and ring connections had been reversed on all four tie-line TRS sockets, and that accounted for the bizarre behaviour that Will had been struggling with ever since the original installation! After eventually tracking down a soldering iron, Paul rewired all four wall-box sockets, connecting the red wire to the tip contacts, the white wire to the ring contacts and the screen to pin 1, as dictated by convention. But on testing the connection afterwards, Hugh discovered that the tip and ring connections were now crossed over because the plugs in the control room had been wired with the white wire to the tip and the red to the ring! So another session of soldering was required to rewire the plugs to the more normal convention. This cured the problem. The original faulty wiring had resulted in the phones receiving either mono or a left/right difference signal, depending on whether they were connected for mono or stereo.
While the wall-box was open, Hugh also noticed that the wiring to the XLR sockets was incorrect — despite the fact that the mics worked as expected, even when phantom powered. The cable screens were wired to pin 3 and the white wires to pin 1, so they had been swapped over as well! It was fortunate, in a way, that the same wiring error had been made in the corresponding XLR plugs in the control room, so at least the wiring did go pin-to-pin correctly and did actually work. However, this arrangement meant that the cables weren't screened properly, and the hot and cold wires weren't twisted together as they should be (so the ability to reject interference was hugely reduced). By this stage, time was against us and there was no way we could rewire 20 sockets and 20 plugs with one soldering iron and no proper tools, so we left Will with a diagram and instructions and gave him a crash course in soldering!
Tracing the source of the wiring issues was time consuming. The wall-boxes had been incorrectly wired, so the team started by rewiring them, only to find that this caused further problems, as the corresponding outputs in the studio had shared the same wiring fault! Eventually, everything was wired up according to convention, eliminating the problems.We also suggested buying a cable continuity/short-circuit tester, as we also discovered a couple of moulded cables that had gone faulty, so once Will has rewired the mic lines he'll be able to check his work.
To test wall-box tie lines and mic lines, first test a suitably long cable that can reach from the wall-box back into the studio. Once you know the cable is good, you can then test each circuit in the wall-box from the control room, by plugging the appropriate control-room cable into the cable tester, along with the long lead from the live room. Once you've verified that the line is OK, you can move the long lead to the next socket and work your way around them all.
Got Glitches
Another very annoying problem Will had been suffering with in the studio was that the Pro Tools system glitched almost every time the lights were turned on or off. In fact, the system lost its word-clock reference, which forced recording or playback to stop each time. We had come across a similar problem on a previous Studio SOS, and on that occasion the problem was a ground loop between the clock master and slave devices, caused by having them powered from different mains sockets on opposite sides of the room. So the first step in curing Will's clocking problem was to check the mains power distribution. We quickly discovered that the computer and LCD monitor were running from a mains socket at one end of the control room, while pretty much everything else was powered from a different socket at the other end. With the addition of another four-way mains board and a few moments scrabbling around under the desk, we had reorganised the mains into a more appropriate star-distribution, with everything now being powered from just one double-outlet wall socket.
The Dynaudio BM6A monitors are good, but a pair of Auralex Mo Pads would provide better isolation from the shelf on which they sat, and would allow the speakers to be angled towards the engineer's head.When we flicked the lights on and off again, it was clear that the system was a lot more stable than before, but it could still be caught out and lose its clock. This suggested that there was probably still some kind of ground-loop problem going on, so Hugh started to investigate the clocking arrangements more closely. He found that Will had configured the system so that the Apogee Trak 2 A-D/D-A converter and preamp was serving as the master clock, running from its internal crystal at 44.1kHz. A BNC-BNC word clock lead was connected to the external clock input of an Audient ASP008 8-channel mic preamp with digital outputs, to clock its own A-D stage, and the S/PDIF outputs from both the Trak 2 and ASP008 were connected to a Digi 002 audio interface, with the input from the Apogee unit selected as the clock reference for the Pro Tools system.
That all seemed perfectly reasonable and sensible, but there was one potential trouble spot. The digital output from the Trak 2 is actually provided on an XLR socket and can be used either as an AES3- or S/PDIF-formatted signal, while the input of the Digi 002 is a standard S/PDIF phono socket. There was thus a potential problem in the way the balanced-to-unbalanced wiring had been done — and, after taking the XLR and phono plugs apart to check the wiring, the problem was immediately obvious. The XLR was wired in the normal balanced way, while the phono plug was wired with the cold wire and screen both connected to the screen contact of the phono plug: this was the ground-loop connection we had been looking for. We unsoldered the phono plug, cut the screen wire back and isolated it, and then re-soldered the cold wire to the body connection and the hot wire to the pin. Like most AES3 outputs, the digital output from the Trak 2 comes via a transformer without an earth connection, so the link to the Digi 002 was now ground-free and floating — and the ground-loop was cured. Frantic switching of the lights failed to cause any clock problems at all, so we declared the system de-bugged! Will ran a long session the same night without the problem recurring.
Will Lamb's Response
"Paul and Hugh made a huge difference in the short time they were here.
"We're a small college but have been lucky to acquire some great kit. However, two of the things that have plagued us since the studio was built have been poor foldback mixes and the computer losing word clock every time somebody turns the lights on or off. Paul and Hugh sussed out the problems in no time, and taught me how to solder to boot! Now it is up to me to sort out the rest of the wall-box wires.
"When the studio was built, we didn't know very much about acoustics, so ended up with a fairly boxy-sounding live room. Paul and Hugh made sensible suggestions that I look forward to putting into practice with our janitor this summer. They also took time to speak to our students, which was a really special opportunity for them. Thanks so much to them for braving the 4am start and gale-force winds to come up and help us!"
Examining Acoustics
Having done what we could to fix the obvious electrical problems, we checked over the control room and live room for other issues. As we had to reach the college by air, we couldn't take any acoustic treatment with us, as this wouldn't fit in the overhead locker or beneath the seat in front, but it was immediately obvious that the Dynaudio BM6A monitors would benefit from a pair of Auralex Mo Pads, as the shelves they were sitting on were none too rigid, and the tweeters were also aimed a little above head level. The Mo Pads would provide better isolation, and would also allow the speakers to be angled down towards the engineer's head.
Reflexion Filters can be very effective. However, they are rather heavy, which can cause problems when mounting them on mic stands. The team rebuilt the support brackets to provide a better centre of gravity and allow single-stand mounting for both the mic and Reflexion Filter. Assorted Auralex panels had been fixed to the control-room walls, which were lined with some kind of perforated rigid panels, courtesy of the company who built the rooms, but as there was no space behind the panels for much, if any, absorbent material, we didn't see how they could be particularly effective. Will said the stereo imaging wasn't as good as it might be, and we quickly noted that there was no acoustic foam to the sides of the monitoring position (the so-called mirror points), so adding more foam there would help. To the left, this would mean obstructing part of the window, but a temporary panel that could be put in place only when mixing would be fine.
The control room (measuring roughly 8 x 8 x 15 feet) was set up widthways, instead of lengthways in the room, to facilitate teaching. This meant that the back wall was very close to the monitoring position, and that the monitoring position was almost exactly in the centre of the room on all three axes. A further window behind the listening position and slightly off to one side connected to an adjoining store room, so reflections from there may well have been affecting the imaging. In fact, we thought it might be beneficial to remove the studding wall to make this storage space part of the control room, although this would necessitate building a sound-isolating box around a wall-mounted boiler.
Because the room dimensions approximated two cubes joined together, they invited disaster, but because of the cold and unremitting wind, disaster declined to attend! In fact, the bass end stayed reasonably consistent as we changed listening positions, which is not always the case when working across the width of relatively narrow rooms. The level of bass did change slightly as you stood up from the listening position, but it wasn't nearly as serious as it could have been. Will agreed to try to fix up more absorbers to the side and to get a pair of Mo Pads to go under the speakers.
Keeping It Live
In the live room, a Neumann TLM103 microphone was set up close to one corner, with an SE Reflexion Filter set up on a separate stand. Reflexion Filters can be very effective, but the mounting hardware is rather heavy and it doesn't put the bulk of the weight over the centre of gravity of the mic stand. We rebuilt the support brackets to provide a better centre of gravity and allow single-stand mounting for both the mic and Reflexion Filter. This entailed leaving out some of the parts and rotating a mounting plate through 90 degrees, as we've done in previous Studio SOS visits. Sadly, the hole drilling wasn't precise enough for us to get all four screws back into place once we'd done this, so Will agreed to make further modifications, using an electric drill, at the earliest opportunity. It was secure enough to use, however, so he tried our new arrangement on his evening session.
The part of the live room being used for recording had been partitioned off using a couple of office divider panels, which, in conjunction with some wall- and corner-mounted Auralex foam, helped produce a reasonably dry environment. The same perforated board was used for the walls and ceiling but, again, seemed to have little positive effect. We couldn't see any evidence of rockwool or other sound-absorbing material behind the wall panels.
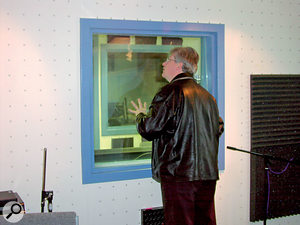
As budget was clearly a concern, we drew up some plans for rockwool slab traps in wooden frames, which could be hung on the walls and across corners to tame a lower-mid boominess we'd noticed at the other end of the room. These utilise an air gap behind the rockwool to increase their effectiveness at low frequencies, and either fabric or foam can be fixed across the front, both to improve the appearance and to prevent rockwool fibres escaping into the air. Fitting these traps across the corners of the room would be the most effective way to use them to reduce lower-mid boominess.
Conventional office dividers only absorb the higher frequencies, because there is very little depth of absorbent material, so we recommended draping them with thick polyester-filled duvets to improve their usefulness and efficiency (we went into more detail on modifying office partitions for acoustic applications in last month's Studio SOS).
The control-room window was an obvious weak point in the acoustic design of the studio, because a lot of sound came through it. In fact, it was quite easy to have a conversation through it! The problem was that the two sealed, double-glazed units (of different thicknesses) were resting on, and pressed up tightly against, the wooden frame: there were no neoprene seals at all, so sound had a direct mechanical path from one side of the glass to the other, not to mention air leakage around the frames! The best solution would be to remove the beading and fix neoprene foam strip along the edges of the glass units to isolate them. However, this could be quite difficult, so instead we suggested using silicon sealer around the edges, to at least make the frame airtight.
Another problem was that the control-room window resonated quite badly, as tapping it in the centre revealed. We suggested damping it with heavy rubber strips a couple of inches wide, held on with double-sided carpet tape.
Mission Accomplished?
Because we hadn't been able to bring any materials with us, the amount of work we could complete was limited, but at least we fixed the annoying electrical problems and came up with cost-effective solutions that Will could apply in other areas once we'd gone. We also spent an enjoyable hour or so talking to the students, and Will seemed particularly happy now that the Pro Tools system no longer threw a wobbly whenever anyone switched a light on or off in the building!
About The College
An aerial view of Lews Castle College in the Outer Hebrides. Lews Castle College Benbecula (LCCB) is one of the premier locations in the UK for studying traditional music. Their programmes are unique in that, whilst they give students a chance to study, in situ, the rich musical traditions of the Outer Hebrides, they incorporate up-to-date music technology and IT in their approach to teaching. They run short courses, such as Digidesign's 'Pro Tools 101' and '110' curriculum, as well as two full-time courses: the Further Education Course in Traditional Music and Gaelic, and the Higher National Certificate in Music. The latter forms the first year of a music degree under their parent university, UHI (the University of the Highlands and Islands). They have 11 Pro Tools workstations, one with Pro Tools HD2 and 192 I/O, two studios with Digidesign control surfaces (002 and C24), and various practice facilities. For further information, visit their web site at www.lews.uhi.ac.uk/gaelicmusic.htm.