Having looked in Part 1 at how to condense your studio setup for use as a live rig, David Harman concludes this short series with tips on how to prepare yourself and your gear for the rigours of live performance.
Last month, I discussed how to select suitable gear to accompany you onto a stage and looked at the process of designing out as many potential gear‑related problems as possible by choosing kit wisely. If you've done this, and prepared the patch and/or sample data that will recreate your songs live, you now need to persuade all your gear to recall all this information at the right moment. Even if you have already decided to use a hardware sequencer to drive your live rig, it is much easier to achieve this kind of preparation using the more advanced facilities of your software sequencer, then download the results to the hardware unit.
Using SysEx & Program Changes
Distinguishing X‑frames from A‑frames is not hard — nor is grasping which of the two is more stable!
In each song, make a space before the start of the note data. This is going to be your preparation space for the rig, in which you will define for each MIDI channel the patches you are going to use and also any associated level or panning messages (more on the latter in a moment).
Synth and/or sampler patch recall via SysEx may sound daunting if you've never done it before, but in practice, if you have a quick look through your manuals, you should find that each device offers a simple means of dumping patches as MIDI System Exclusive messages, which you can record into your sequencer and play back later to recall the patch. Older synths may only offer you the option to dump the entire patch memory as SysEx; obviously from an on‑stage time point of view it's better if you can recall patches on an individual basis, loading only those you need rather than the entire sound set as it was on the day you finished the song.
Of course, you might prefer to arrange it so that all the sounds you require for your gig are already in your synths' and samplers' memories. This means you don't have to tangle with SysEx at the start of each track, but consider whether this approach is really as sensible as it sounds. If all the patch info is stored in the song sequence, it will be automatically recalled every time you play the song, and is guaranteed correct for the song each time, even if the patch has been reprogrammed by accident before the concert. This not only means you can now play the set in any order, it also means you can return to these tracks at any time in the future and the synths will be ready to play back the track.
There's another significant advantage to using SysEx, too. If you rely on a device's memory and its internal backup battery fails before the gig (or worse still, in the middle of the set!), all your carefully crafted or edited patches will be lost, and you will have no means of recalling them at the gig — a truly daunting prospect, and one which could completely ruin your concert. If the patch data is stored with each song, however, you just smugly press Play and your sequencer will do the rest for you.
If you decide to involve SysEx (and in my humble opinion you'd be mad not to), the idea is simply to record all the necessary setup data into the preparation space at the front of your song, well before any note data is transmitted. Exactly how long you should make the space will depend on the gear you are using and how much SysEx you are intending to send. I've always used about 20 seconds, and that's proved fine in almost every case, provided that only individual patches (and not entire banks) are being uploaded to each location.
Even if you insist on having all the required sounds already in the synths' memories, it is still advisable to dump a complete SysEx stream of each device in the rig into individually‑named sequencer 'songs' containing just the SysEx data for one machine each, as a failsafe backup.
Once the appropriate sample or patch data is uploaded to each synth, you need to select the required patches for each MIDI channel. Exactly how many MIDI Program Change messages you will be sending depends on the method of patch selection and operational mode of each of your synths and samplers, but you are most likely to need a single Program Change to be sent on each MIDI channel being used. Some samplers will allow Load commands to be executed by Program Change messages, but you should ensure that the length of your preparation space accounts for any loading time and subsequent program changes.
Although putting all the channelised Program Changes together in one heap will work fine, something that I find useful is to stagger the various messages so that they hit the rig elements in a defined sequence at intervals of about one second — so all the changes for each unit are sent together, but unit‑to‑unit there is a delay. This gives you time to scan across the rig as each unit receives its changes, and check that they have been received correctly. Program Changes are, on the whole, very reliable, but I have had a couple of embarrassing instances that have persuaded me that it's worth checking each time. Hearing your searing monosynth lead line playing on a detuned, heavily reverbed marimba is a disappointment that has to be experienced to be fully understood...
One other warning about Program Changes: some devices take longer to reset than others, and in some cases, even when a display says the sound is 'there', it may be a second or so before there's any chance of hearing anything out of that unit. MIDI‑converted analogue synths with memories can be particularly sluggish in responding, and sometimes seem to have their own opinion on whether they should be recalling the patch you asked for or a completely different one — all the more reason to keep an eye on things.
Once you have the appropriate sounds in place, it's time to set the levels and pans. These are only the initial settings, of course. Additional pan and level data may be thrown at any device during songs, as may additional Program Changes.
Note that is important to enter the SysEx, Program and Pan/Level data in the order described above. In some cases you might get away with another order, but some devices will reset MIDI volume levels when they receive Program Change messages, or leave the 'old' sound in memory after a SysEx dump if a new Program Change is not received afterwards to call up the new patch. The above order should work in almost all cases.
Rack 'Em Up
Live techno veterans Orbital make a virtue out of necessity by using their highly practical head torches as a visual focus in their live gigs. On a darkened stage, there is frequently nothing to be seen but the beams of their headgear bobbing eerily through the dry ice... very cool indeed!
Your next task is to arrange your rig into a transportable, fault‑resilient package.
The first consideration is flightcasing. The live environment contains many dangers for studio gear, such as heat, liquids, and the threat of impact, and good casing helps prevent unfortunate occurrences. At particular risk are rack units and sequencers, which also suffer from the threat of theft. Racking units properly makes the job of the would‑be thief that bit harder, and gives your kit a fighting chance of surviving the night intact (for more on this, see the 'Case For Cases' box elsewhere in this article).
If you follow my advice and rack all the gear you can, you can then take advantage of all that real estate that's wasted inside the rear of the rack. Just how much space you have available back there will depend on the depth of your modules, but in most cases you'll probably find that there are at least a few inches to play with in all four planes (top, bottom and sides). This should be plenty of room for power, audio and MIDI cables, plus cable‑tidying apparatus. You might also consider leaving the bottom 1U of your rack unused, in order to leave space for coils of excess cable and power supply blocks.
The watchwords here are 'tidiness' and 'accessibility'. The cabling needs to be secured so that it is easy to troubleshoot and less prone to accidental removal by cable tugging. It also needs to be accessible in a hurry: when you need to move a MIDI lead to another piece of kit elsewhere in the rig, you won't thank yourself for fixing it to the rack using industrial staples and epoxy resin.
First on the list of cables to consider are those that carry your mains power. Not personally having access to the mysterious technology that allows gear on certain TV programmes to produce great results without being plugged in, I have found that most of my rigs worked better when firmly connected to the mains and switched on.
As always, you should make sure that you are ready for the worst possible case. That is, have the means to power all your devices from just a single socket if necessary (current rating allowing). Even on a professional stage, where the sound engineer might well break out a number of sockets close to your position, it's very unlikely that there will be enough to power every unit independently. There is no sadder sight than a performer wandering from person to person while you're all setting up asking whether anyone's got an adaptor.
If your equipment is to live permanently in this rack, and your budget allows, it is well worth considering a rackmount mains distribution unit (see the 'Power Struggles' box above). Since one of these can set you back a couple of hundred pounds, you may prefer to stick to four‑way socket extenders or power blocks, and, space allowing, these will do just fine, but avoid the type with switches built in, as these add an unnecessary risk of accidental switching. It's still worth physically attaching these to the rack, as all the mains cabling is then kept in the rack and away from roadies' shoes, thus saving it from being pulled out by mistake. What's more, when you get to the venue, you want to be able to remove the back door of the rack, spool out your one mains lead and plug it in, not faff about with 17 different plugs.
My preferred method of securing these blocks is Velcro with the self‑adhesive reverse side, as they can then be easily moved elsewhere if you have to. As for their position, one vertically on each side is ideal. Although you can use the base of the rack, this is inadvisable when using more than four devices, because you'll end up 'two blocks deep'; once all the other cabling is in place, getting to the rear block in a hurry can then prove a major pain. You can also risk accidentally prising one of the rear plugs loose when removing a plug from the front block.
The next cables to consider are the audio and MIDI ones. If your rack is very tall (above 10U) you could consider mounting some skeletal cable trunking down one side. This has flexible plastic fingers that are arranged like a rib‑cage, and cables can be added to or removed from the trunking at any time, and broken out to modules at any point.
Whether or not you employ trunking, you will probably end up with too much cable. This is best handled by loosely coiling the excess and tying it with cable ties (see 'The Ties That Bind' box) before dropping it into the space that you (might have) left at the base of the rack. Don't cut cables to length unless you are sure you will never need to use them anywhere else in a hurry.
Synths — Positioning & Security
Without proper cable ties, the bottom of your live rack could look like this...
You've now got a rack that can be transported easily and safely, so on to your keyboard synths. You've probably already got stands for these, which may be of the 'X‑frame' or 'A‑frame' type (it's obvious which is which — see pictures, right). Either will do fine, but an A‑frame stand is my own preference for live work, as it offers so much flexibility of angle and mounting style, and also leaves space directly underneath the keyboards for pedals and monitor wedges. Do make sure, though, that you've got a spare of the tool(s) required to put the A‑frame together if the bolts are of the recessed type.
The gaffer tape that you'll have with you (see the 'Essential Toolkit' box elsewhere in this article) will ultimately be used to secure the synths to the stands. Although gravity is on your side, over‑eager roadies or sound engineers crawling around on the floor or other band members jumping around the stage can result in synths getting toppled off their stands and suffering a sad demise.
Only you can decide how you want your rig to be arranged. From an operational perspective, though, it's important to make sure that any important displays can be seen at any time from your main playing position. Make sure also that your sequencer is clearly visible at all times, and that its control surface is free from any unnecessary clutter.
Depending on how close you will be to any public areas and the access restrictions that apply to the stage, security may also be a big consideration. If you are using a hardware sequencer, bear in mind that they are compact and therefore eminently nickable. You may find it useful to mount it into a lockable rack drawer. These cost about £60, and in order to mount the gear simply and safely, it's a good idea to get a block of foam to fit the drawer (the rack/rack drawer supplier should be able to get this for you). If you're using a software sequencer, rackmount kits are also available for computers — ask the rack supplier for their recommendations based on your particular computer.
Rackmount modules themselves can be mounted more securely using rack screws with a 'security head'. This is essentially a normal screw, but the head is domed to prevent attack with pliers, and the screwdriver slot is replaced by a special Allen key locator, with a central pin that prevents use of an ordinary Allen key. These are certainly more secure than conventional screws, but you may feel that the risk of losing the key and being unable to get the kit out of the rack until you find another one outweighs the risk of someone nicking the gear...
Data Backup
It is absolutely critical to create and test a reliable backup data set for the entire rig. Internal memory backup batteries can fail, Zip disks can get trodden on and trashed, and hard disk drives can happily crash with or without external influence. Any or all of these could ruin your evening, so be prepared.
Your backup should include your sequencer data (on floppy disks or SCSI hard disk), your synth patches (stored as SysEx in a sequencer or on memory cards) and sampler data (internal hard disk backed up to removable media). Mark all backups clearly (for use in low‑light conditions) with the device for which they contain data, the date they were created and any appropriate set/song names.
Remember that you'll need immediate access to this data if there's a problem, so it'll have to be close at hand. If you've mounted your sequencer in a rack draw, consider cutting out more foam and making cubby‑holes for the various data backups. If not, package the backups together in a single box that can be kept near you. A tough plastic case with foam can be useful for this — they cost about £40 including the foam blocks, and are sturdy and light.
Testing, Testing...
The HZ Audio Octopuss mains distribution unit offers a mixture of IEC outlets (visible on the left), as well as connectors for units usually driven from wall‑wart power supplies.
It's time to take a deep breath, disconnect everything, and build your entire rig exactly as it's going to be on the night. Although it might seem like overkill, this is an essential part of preparing any rig for the first time. However well‑prepared you think you are, it's amazing just how many little bits and pieces can be ironed out well in advance by going through the set 'for real'.
Disconnect all your equipment to the level that will be required for transport (so, for example, leave the plugged rack cabling intact if it is to travel in that manner). Find yourself a space to build the rig — ideally this should be in a different room so that you can be really strict with yourself about what you've 'got with you' and what you have 'left behind'.
Get all the kit into the required spot, and darken the room if possible to simulate stage lighting — a small table lamp in a large room is about right. You'll probably have much better lighting on site, but now is the time to practise in the worst‑case environment. If you're feeling brave, you could try pitch darkness, but I've only ever twice had to do that in the real world. The point of the darkness is twofold: you will get used to holding a torch while constructing, and find all sorts of problems that only come to light in a dark room — if you see what I mean.
You might not think you need to learn how to use a torch, but remember that you're probably going to need both hands for a lot of the work, especially high‑speed cable troubleshooting. As a result, the torch is probably going to end up between your teeth (another very good reason for having your own torch...), between your shoulder and neck, or between your knees. Only practice will tell you which tasks require which pose, none of which is very attractive or comfortable. The alternative is to do what live techno stalwarts Orbital did and get head‑mounted torches (see pic above). These are great for cable work, but can be harder to get into nooks and crannies. If you are going to be playing live a lot, and your rack is a major part of the rig, you might consider a racklight — a 1U rackmounted light that slides out for use and retracts for transit.
You will very quickly discover some nasty things about working in the dark. Human feet seem to be designed specifically to get caught up in cables, power switches are in the strangest places, and synthesizer port labelling, on the whole, is very small and on the back of the unit rather than the top.
The first two issues you're pretty much stuck with, but the third you can address. A reel of white PVC electrical tape and a permanent black marker pen will serve you well. For keyboard synths, run tape along the rear of the top, and mark the position of all ports and switches that appear on the back, including card slots and pedal inputs (oh alright, you can turn the light back on for this bit...). You might even want to do this on units that already helpfully print this info on the top, since manufacturers conspire to employ only the world's smallest fonts for these legends. In addition, it's a good idea to mark each unit with a MIDI channel identifier (and port for software sequencer users...). Although I'm sure you could reel off every channel of every device right now, this information can flee your mind at the first sign of trouble
— so mark 'em up.
MIDI channel labels are a good idea on rackmount gear, too, along with any SCSI ID numbers. It might also help to put label tape by certain vital keys — for example, those marked Load, Menu, or MIDI — and the Volume control.
You might also consider labelling cables. For some people, this is an unnecessary annoyance, since it means finding the correct cable and not just the correct type. For others, it is their guarantee that they have all their necessary cables. I do prefer to label, but only with a type reference and unique number, which must be the same at both ends — 'M18' for a MIDI cable, for example, or 'A18' for an audio cable. The 'M' or 'A' reference means that if the connector is obscured, you can still determine its type. The number is of course for troubleshooting purposes, so you can see where the cable is plugged in at both ends, even in a rats' nest of wires.
Once the gear is marked, turn the lights off again, complete the build and run the set. If you have the appropriate kit to hand, try recording the set, as you can pick up problems during later playback that you were too busy to notice during the set. If all is well, run the set again — but this time from the backup disk/card sets. It can also be a good idea to run the set out of order at least once, especially if you are sending SysEx, to make sure that the equipment is being set up properly for each song, and not just inheriting the correct settings from the previous song.
Once the set runs satisfactorily, get someone else to mispatch a couple of MIDI or audio cables and disconnect a couple of others while you are out of the room. Return to the rig, press Start on the sequencer, and see how long it takes you to notice, identify and rectify the problem(s). This can prove invaluable practice, especially if other bands are to be performing on the same stage as you during the evening, or the gear is to be set up within reach of the crowd (as in a pub). Cables can get pulled out, repatched, shorted or 'borrowed', so it's a good idea to practise spotting the symptoms.
Just a few items left to remember. First, spares: take at least a couple of extra cables of each type (MIDI, audio and SCSI), and fuses of any type you use. Extra mains leads are also a must, as are spare batteries for any device that needs them.
Make multiple copies of your setlist, printed or written in large letters such that they can be gaffer‑taped to the floor and read without you getting on your hands and knees. The copies are for the sound engineer and any others who may need them. They may not know the names of your songs, but they can count each one as it passes and so gauge progress.
Finally, a thin, dark‑coloured sheet with which to cover your gear once you've set up will help avoid dust, spillages, uninvited tampering and, to some degree, theft. It must be thin, though, otherwise you risk your gear overheating.
On The Day
The gear's ready, your lamé suit is looking fantastic, and you're ready to take your music to your public... but the preparation has to continue. When you arrive at the venue, your first mission is to find three vital pieces of information: the timetable for the event (what time is rehearsal, when does setup finish, when do the public arrive, when are you on, and so on), the situation regarding sound and mixing (if you have not been able to establish that in advance), and the situation with mains power (where will you obtain it, and is it active now, or do they have to throw some breaker switches for you first...?).
Don't presume anything. Always find the person at the venue who is responsible for the technical side of the event, and ask them the questions. Depending on the size of the gig, this may be anyone from the pub landlord to a professional Production Manager, but let them know who you are, and that you're prepared to work with them to make the evening go well.
The same goes for sound engineers, if there are any. Locate them, discuss what they intend to do, and how it compares to what you had in mind. Give the engineer(s) a copy of your setlist, and explain any intro CD/MD playback you have planned. Some give and take may be required. Also, ensure you use the power sockets the engineer tells you to. Do not plug any of your kit into other sockets in the room (see the 'Mains Street' box for the reasons why).
Once the system is up and running as required, cover your rig as best you can with your thin sheet(s) while other bands (if any) soundcheck. Once they've finished, run a couple of songs in your headphones (check that your send to the engineer is muted at your end or theirs) to ensure that nothing has changed during soundcheck.
Curtain Up
Deltron's MIDI Brighteye — a great budget alternative if you can't stretch to a fully fledged MIDI analyser
The big moment. Go on stage and give it everything, knowing that you've prepared for everything you possibly can. If it goes well, you'll have the time of your life. There is a unique, visceral excitement in hearing your music playing through a large sound system to a crowd — and live performance can throw up all sorts of ideas and sounds that might never have occurred to you in the studio. Whether these happen accidentally or not, they are beautiful moments indeed.
If there is a problem, hopefully you'll be able to resolve it and move on, but remember that there are some situations for which you can't possibly prepare, and there is always a chance that a concert will be a disaster. Most people experience gigs like that at some point, so don't give up — learn from it and cover that eventuality next time if you can, or just put it down to experience if you can't.
In short, as a live sound engineer once put it to me, "Don't be afraid — just be ready...".
The Ties That Bind — Cable Ties
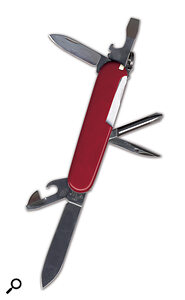
If you are not working in silent spaces (for example backstage theatre rig construction), velcro ties are arguably the most convenient type available, as they are easy to attach and detach at speed, even with freezing cold hands. For the type that can be fixed to the cable at one end then wrapped around a whole bunch of cables and secured, you're looking at about 90 pence each.
These are preferable since they are retained on the cable even when untied and therefore don't disappear so often. They are not cheap, however, and if you're using a lot (or if the tearing noise would be a problem), you could stick with more usual 'pull‑through' plastic ties (about £7 per 100). These work fine, but make sure you use the 'releasable' type. All types can be undone by determined individuals, but the 'releasable' ties have larger, finger‑operated release clips instead of the small clips that require a flat blade to get them open.
Power Struggles — Mains Distribution
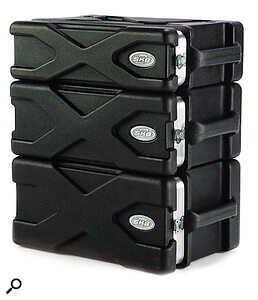
A great way of distributing mains in a rack is to use an IEC320 Rackmount mains distribution unit.
These units connect to the normal mains supply and break it out into multiple six‑Amp IEC320 sockets. These are much smaller than conventional 13‑Amp plug sockets, as you can see from the picture shown here of the HZ Octopuss mains distribution unit reviewed in SOS July 2000 (note: the Octopuss included other mains connectors too, but you can see its four IEC connectors over to the left of the unit's rear panel). The difference in socket size means that some IEC distribution units can offer 12 or more outlets in just 2U of space. They are usually very shallow units (100mm or so), so if your rack has rear‑mounting brackets, the distribution unit can be mounted at the back to avoid wasting valuable rack height on boring old mains. Connection from the unit to each piece of racked gear is via an IEC extender lead (about £5 each).
For kit that has a captive mains lead, you can exchange the existing standard mains plug for a 6A IEC320 plug (about £2 each). Most synth sound sources are well within that current limit, but you should of course check that the unit you are adapting draws under six Amps. The beauty of this arrangement is that it's tidy when in the rack, but should you ever need to use that piece of gear elsewhere, you can connect it just like any other device, using a standard IEC mains lead (oh alright, kettle lead) plugged into the flying socket.
The only downside of using IEC distribution units comes when you suddenly need to add another piece of gear to the rack, and that module has a 13A plug. Many IEC distribution units have at least one conventional 13A socket on the front panel (the IECs are usually rear‑mounted), but it's worth checking that the unit you choose has this facility — the Octopuss shown below doesn't, for example.
The Essential Live MIDI Toolkit
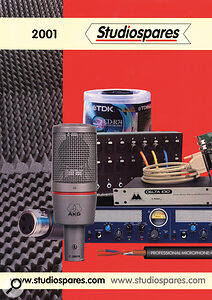
- GAFFER TAPE
Gaffer tape is an essential item. The choice of discerning hostage‑takers everywhere (according to Hollywood, at least), Gaffer tape is strong, but easy enough to tear by hand when removing lengths from the reel. It can be used to secure kit such as stands, cables, and sequencers. It is available in various colours, but black is usually the best for live work. In theory, it can be removed without leaving a residue, but don't risk your vintage monosynth's fine wood finish putting that to the test.
• TORCH
The torch is arguably the most important tool to the Live rig user. You won't have time to borrow one when the proverbial hits the fan, so spend some money and get yourself a solid, compact unit that either fits into a pocket or for which you can buy a belt holster. The torch needs to be with you at all times, so get used to carrying it. Some models can also accept a hexagonal rubber shield at the bulb end that is great for stopping the torch rolling off uneven surfaces, and allows the fixture of coloured plastic filters for a more subdued beam.
• MIDI ANALYSER
These little gadgets can be lifesavers when troubleshooting. Usually just a pocket‑sized, battery‑powered box with some LEDs and MIDI connections, these can tell you the content of a MIDI stream (the channel of incoming data and the data type, for example note information, program information, and so on) so that you can at least check what data is hitting a particular unit. They cost around 30 to 40 pounds, and are particularly handy when dealing with keyboard synths, which rarely feature a MIDI In LED. It's also good practice to keep a pair of MIDI cables that are known to work specifically for use with this unit .
If you can't stretch to one of these, and can put up with knowing merely that MIDI data is present without being able to tell exactly what type it is, an excellent budget alternative is Deltron's MIDI Brighteye (shown above) which will plug into a MIDI socket and at least show whether MIDI data is present on that connector or not — if so, the LED at the end of the Brighteye lights up. Brighteyes are available for around £7 each.
• MULTI‑TOOL/PENKNIFE
You'll need a pocket‑sized gadget that can at least cut, deal with screws (both standard and cross‑head) and ideally act as pliers for crimping or pulling. As with the torch, choose one with a belt holster if possible.
- PVC TAPE & PEN
White PVC (or 'electrical') tape and a black marker pen are invaluable for naming channels, cables, modules, and so on. The tape can also act as an insulator when addressing cable problems.
- HEADPHONES
A good pair of headphones will prove invaluable in troubleshooting. Not only can you work without disturbing others, you can also plug directly into the headphone socket of any device that is causing trouble and hear just the output of that one unit. If your mixing desk doesn't have a Solo function, this one factor alone might save your bacon one day. Try to find a pair with good rejection of external noise — the 'closed' designs are usually preferable for this reason.
Mains Street — A Safety Warning
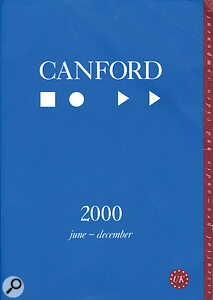
Power is a very complicated subject, and could take up a two‑part article in itself, but there are a couple of basic points that should be mentioned here.
First, and most importantly, when it comes to power, if you are not absolutely sure what you are doing, then don't do it. Whether you're just changing a plug or plugging your entire rig into the house power system, ask someone who does know. Nobody will ever think less of you for asking — quite the opposite in fact. Furthermore, most larger venues are required to have their own house electrician, and you should never make (or be asked to make) changes to any electrical wiring beyond your own rig.
Second, if you experience hums and buzzes when connecting up your rig, well‑meaning individuals might suggest that you remove the earth connection from your mains plug, as "most hums are earth‑related". Under no circumstances should you do this. On most audio equipment, there are two ground systems — 'chassis ground' and 'audio ground'. Audio ground is what those people are usually referring to when they talk about grounding problems, and most problems of this type can be addressed successfully and safely using various audio wiring tricks. The chassis ground, however, is a mains safety earth connection, and is there to protect you in the event of a failure inside that device that could result in mains power running around the metal parts of your gear, or even the casing. Important in the studio, the mains Earth connection is vital in the live environment where there is a greatly increased risk of shorts, miswiring and other disasters. Removing it therefore puts you and everyone around you in serious danger, and should never be considered an option. Yes, people have got away with it, but that's down to sheer luck rather than good practice.
When connecting your mains, also bear in mind that just because you can see some wall sockets on the stage doesn't mean they'll be used that evening. They may not even be active at all. Furthermore, plugging into these could be extremely dangerous, as the venue may well operate a three‑phase mains supply. The sound department and lighting department usually operate from separate phases on such a supply so that they are independent of each other and each has their own 'clean' supply.
This is good news from an electronic noise point of view, but also brings its own dangers. Without going into the details, there can be a massive potential voltage across two different mains sources (up to 415V in the UK), and in the event of a piece of equipment failing or being miswired, this difference could prove fatal. A simple rule of thumb is that all sound equipment and anything connected to it should be on the same phase.
The Case For Flightcases
When it comes to flightcasing, I feel it's time to get on my soapbox (also flightcased, naturally).
Some consider flightcasing an expensive luxury, while others always factor a good case into the price of any new piece of gear. It is a simple fact that many catastrophic and non‑catastrophic equipment failures in the live environment come about as a result of poor protection.
A reasonable 8U 'semi‑flight' designed rack unit with front and back access is going to set you back about £200. Granted, it doesn't make any sounds, and that £200 could have been a Sequential Six Trak or an SH101, but given the money you've invested in your kit, the idea of spending £200 on protecting four or five units on the road and getting a rather suave‑looking studio rack into the bargain should make perfect sense.
By all means take the units naked and unprotected, but don't complain when a careless roadie drops a stage light onto your gear, turning your 3U sampler into a 1U blanking panel.
Useful Contact Details
Pretty much anything you'll need to put a good MIDI rig together (including everything mentioned in the 'Essential Toolkit' box with the exception of the penknife) can be found in the catalogues of general pro audio equipment suppliers, such as Studiospares and Canford Audio (see contact details below). As well as the basic accessories, these companies carry all manner of gadgets and gizmos that solve problems you didn't even know you had. Ask them to send you a catalogue, and you'll see what I mean...